Why use
for concrete?
The Benefits of using graphene in concrete
Mechanical Enhancements
- Increased Strength: enhance the tensile, compressive, and flexural strengths
- Improve Hydration rates and refine microstructure
Durability Improvements
- Resistance to chloride permeation and hence corrosion protection
- Improvement in shrinkage
Environmental Impact
- Lower Cement Usage: decrease amount of cement by up to 20%+ without compromising structural integrity
- Reduced Carbon Footprint: enhanced mechanicals can lead to a reduction in CO₂ emissions by 30%+
- Allows the use of more SCM without compromising strength development
Economic Advantages
- Improved Economics due to reduction in cement along with improved strength
- Shortened Curing Time: graphene accelerates the hydration process, reducing the curing time
Product – Features:
- GenableTM Decarbonizer is a graphene-based liquid admixture.
- The admixture is formulated with dispersing ingredients to enhance the graphene performance.
- The surface-functionalized graphene create strong bonds at the interfacial transition zone between the cement paste and the aggregate.
- Improved compressive strength that allows for reduction in total cementitious content.
- Order of addition matters: introduce GenableTM Decarbonizer into the concrete prior to addition of other admixtures.
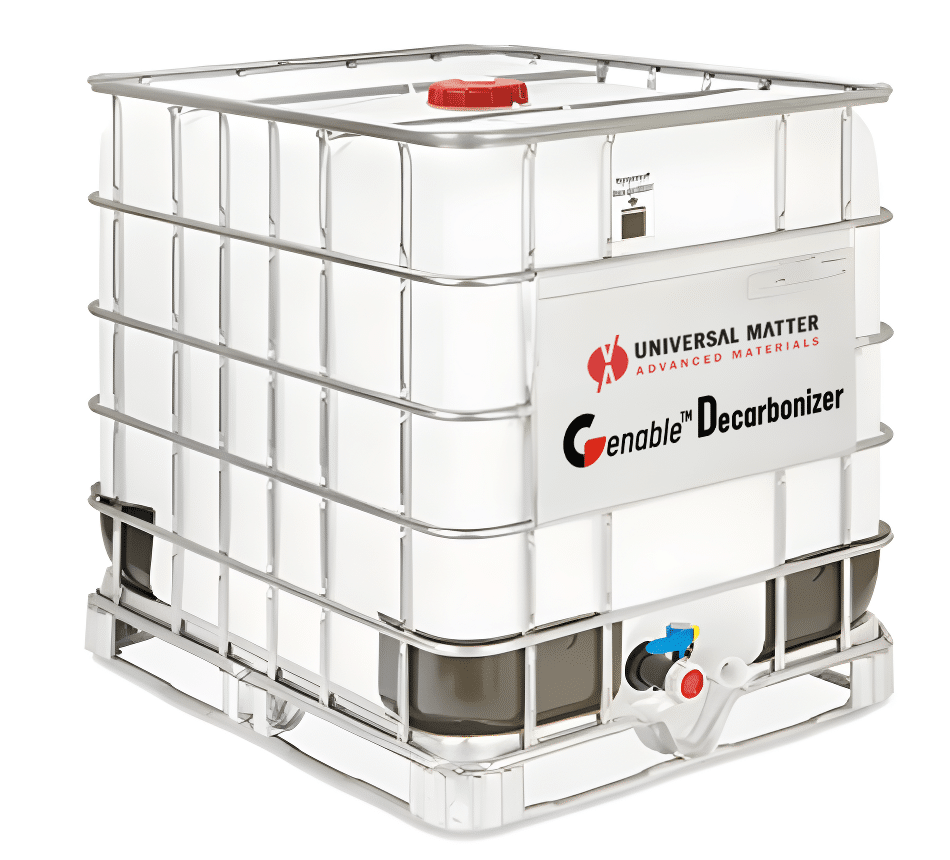
Properties | Range |
---|---|
1Viscosity
|
2,000 – 4,000 cp @ 1/s |
2Storage temperature
|
5-40 °C |
3Dosage
|
300-500 ml/100kg cementitious material |
Mix Design possibilities with 
Reduce carbon footprint: increase compressive strength to M80 without adding cement = save 100 kg cement = 80 kg CO2/m3 concrete
Recommended

Dosage: 2.5 kg = 2.0 liters/m3

Dosage: 2.5 kg = 2.0 liters/m3
Example: M60 Concrete Mix Design:60 MPa (8,700 psi) = ~500 kg/m3 cement
Add
300-500 ml/100kg cementitious material
Product – Features:
- 0.5% w/w cement
- 300-500 ml/100kg cementitious material
- Density: 1.25 kg/liter
Reduce carbon footprint:
increase compressive strength
to M80 without adding cement = save 100 kg cement= 80 kg CO2/m3 concrete
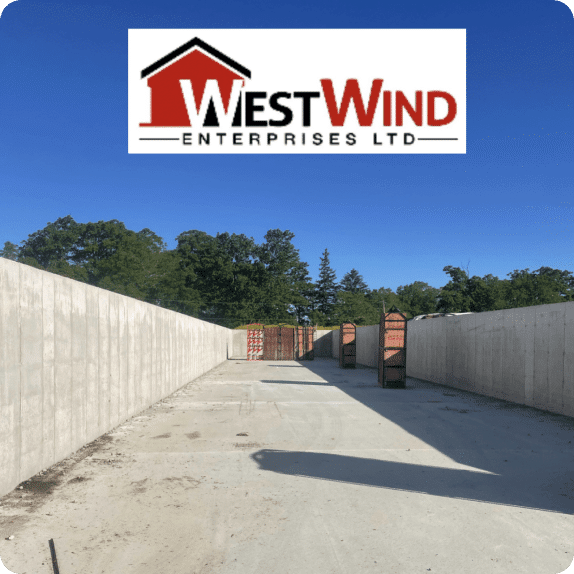
Commercial projects with
Horizontal Silage Bunkers
Examples of commercial project completed in 2024
- Floors 30 MPa concrete, walls 25 MPa concrete
- Both with 15% cement reduction in mix design
- Benefit: improved durability of concrete to reduce lactic acid attack from corn silage fermentation
- Completed construction of 15 silage bunkers since May (total of ~4500 m3 of concrete)